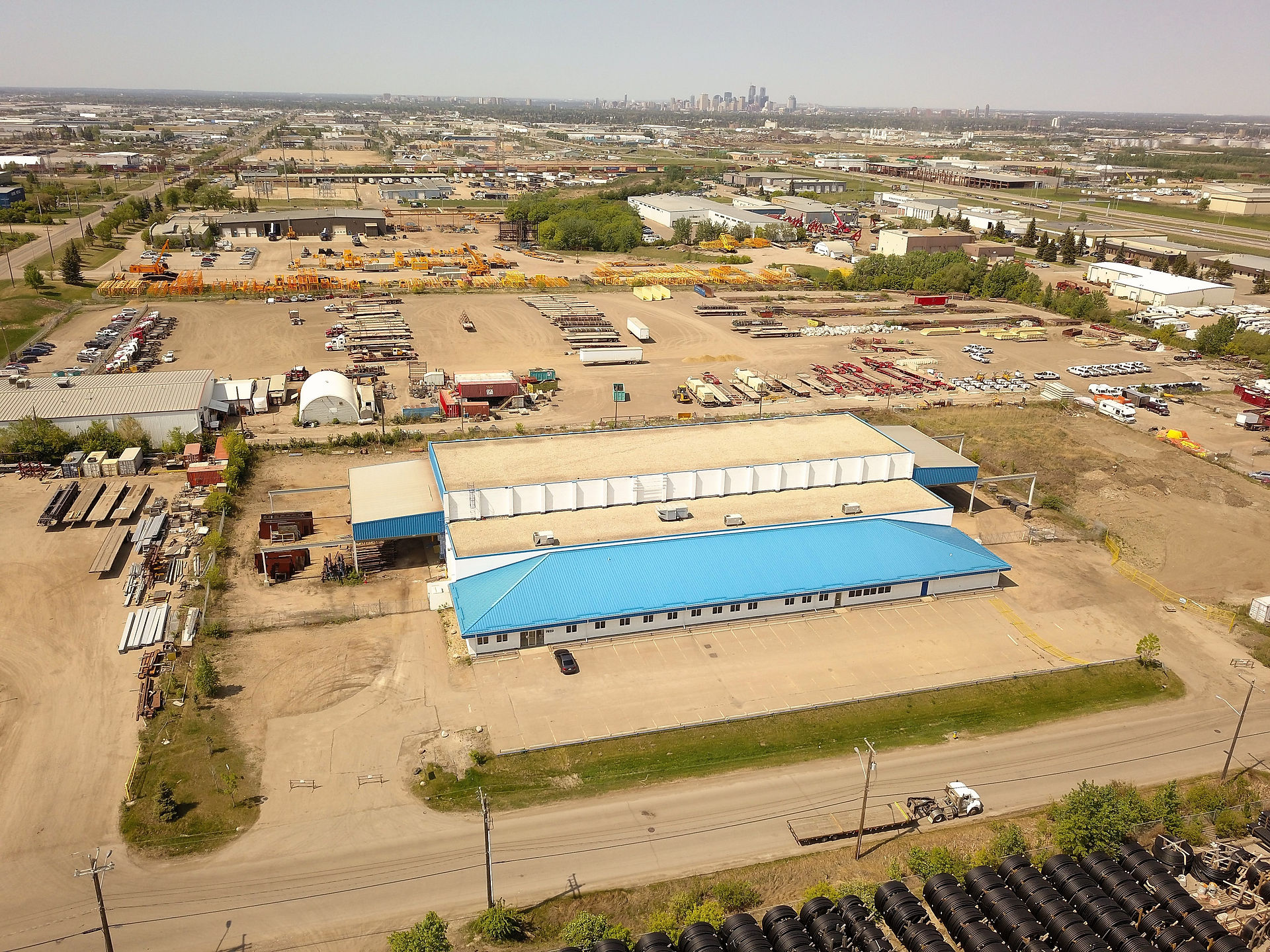
Concrete
The fabrication and machine shop are constructed of a load-bearing concrete masonry-pilaster-lintel-insulated-masonry-infill wall system, the pilasters being 15’ on centre providing for overhead crane rail and roof structure support. The wall system incorporates air and vapour protection through the proper application of an Alkyd based paint on the interior and latex paint on the exterior (a repaint with a special thermal latex coating is scheduled for this fall or next spring). The concrete grade beams and floor slabs include extra steel reinforcing capable of supporting heavier than typical loads.
Roof
The roof design is a metal deck finished with an insulated EPDM roofing system and supported by open web steel joists. The office portion of the facility has a wood roof truss system supporting a sloped roof design finished with a standing seam metal roof system. The exterior of the office area is finished in stucco.
Windows
Exterior window units are anodized aluminum with clear glazing. A double entry door system is at the main entrance to the office area. Access to a corridor leading to the machine shop and lunch room is also available from the front of the building, as is direct access to the locker/wash/change room.
Doors
Along the south perimeter of the facility, a 15 foot by 16 foot powered overhead door and a man-door provide access to the machine shop. Two 20 foot by 18 foot specially designed bi-parting sliding doors provide access to the fabrication shop, one on the southend and one on the north-end. Along the rear of the facility (west side), two man-doors and an 18 foot by 16 foot powered overhead door provide additional access to the fabrication shop as well as one additional man-door on the north perimeter. A 10 foot by 12 foot powered overhead door and a man-door along the north perimeter of the machine shop provides access to the parts and tool crib area situated adjacent to the machine shop area. Loading docks are at grade level.
Work Stations
The machine shop includes a foreman’s office next to the parts and tool crib area. The fabrication shop includes a clean assembly/paint room and paint storage room. Work stations along the east and west walls of the fabrication and machine shops each have a complete distribution system for four process gases (carbon dioxide, oxygen, propane and compressed air) and 110 volt, 20 amp duplex receptacles on dedicated circuits.
Paint Shop
A roofless open top paint shop allows crane access for placing and handling materials. Regular overhead lighting is supplemented with wall-mounted lighting, with rails embedded in the floor for carts to facilitate the movement of heavy machinery. There is also a ventilated paint storage room adjacent to the paint shop.
Mechanical
The office is serviced by two heating and air conditioning roof top units. The shop areas are heated by gas fired radiant tube heaters and are kept clear of cutting and welding smoke via a special 30,000 CFM make-up air and exhaust system. The building features a 3 phase, 1,600 amp, 480 volt service.
Cranes & Crane Rails
The building, being designed specifically to facilitate the steel manufacturing of heavy equipment attachments, includes an extensive system of cranes and crane rails entailing a total crane rail length of 2,160 feet, designed to accommodate 10 cranes, 8 in the fabrication shop and two in the machine shop. Special engineered crane rail mounting brackets were built into the concrete pilasters with precision. The fabrication shop crane system is a unique design incorporating two layers to facilitate an efficient steel manufacturing process. The top layer accommodates two parallel crane systems running the full length of the fabrication shop with three 5 ton cranes on a 40 foot span and a 15 ton and 5 ton crane on a 30 foot span, all with under hook clearance of 21 feet. A 3 ton monorail crane is suspended between the top layer crane systems. On the lower layer, spanning the full 70 foot fabrication shop width having a 17 foot under hook clearance, are two 5 ton cranes, each able to travel 80 foot out of each end of the fabrication shop to bring in raw material and take out finished product. One-half (40 feet) of each 80 foot outside crane rail section is covered with a metal roof system complete with panel rib skirting to protect the crane ducto-bars from the elements. The design allows for covering the other half in the future if the need arises. Specially engineered vertical-lift powered crane door systems with positive weather seals are included which allow the passage of the lower level 5 ton cranes from the interior to the exterior crane runways and are designed to drastically reduce heat loss due to infiltration.
Raw Material Storage
Approximately 75% of raw material storage is outdoors, 25% indoors (with 90% under bridge cranes).
General Shop Flow
There is a general south-to-north flow. Raw materials enter or are stored at the south end; materials are then cut, with some diverting directly into the machine shop and some proceeding down the fabrication shop for fitting and welding. Some of the sub-assemblies continue through the fabrication shop, while some divert to the machine shop. Machined parts return to the fabrication shop at mid-point, sub-assemblies are painted, and machined / non-machined sub-assemblies and machined parts are assembled.
The final fit-up and hydraulic connections are made near the north end of the shop, with final painting and cleaning performed before placing outside the north end of the facility for shipment.
Air Management
The atmospheres of the office, machine shop and fabrication shop are designed to maintain separation. Component parts receiving and storage are covered by cranes for movement into the machine shop; the office is slightly pressurized with double door vestibule separation between the office and the shop to eliminate shop dust and smoke incursion.
The shop make-up air system discharges into the machine shop. Open forklift access routes and wall fans push clean air into the fabrication shop, while wall-mounted exhaust fans on the far side of the fabrication shop draw air away from the machine shop and discharge dirty air to the outdoors.
The paint shop exhaust system interlocks with the makeup air system and wall exhaust fans.
Shop Lighting
Lighting levels are maintained by ceiling-hung industrial lighting throughout the fabrication and machine shops. There is also wall-mounted fluorescent lighting along the side of both shops to reduce shadows on the underside of work stations, with washable white interior paint on the shop walls to enhance lighting.
Piping and Electrical
Pipe manifolds distribute bulk gasses and compressed air throughout both shops: these are located every 15 to 20 feet along the east and west walls of both shops, with pipe drops for oxygen, fuel gas, shielding gas and compressed air. There is wiring for 110V duplex receptables and 480V 3-phase disconnect and plugs. There are also under-floor conduit pipes for delivering gasses and electrical connections to temporary mid-shop workstations.
Shop Staff Amenities
The facility is complete with a large, brightly finished lunchroom with ceiling tiles, painted walls and kitchen counter, a large locker room with shower and wash-up area, separate ladies' bathroom and change room, a dedicated first-aid room and separate staff entry door with direct access to locker areas and shop entrance.
Yard
The yard is properly sloped, compacted and graveled for all-season use by heavy trucks, with through-yard circulation for semi-trailer trucks to avoid having to turn around to maneuver. There is additional exterior lighting to allow for safe nighttime access, fully fenced with chain-link equipped with lockable truck passage-sized gates. There is also a paved parking area with block-heater plug-ins at the front of the building to accommodate all staff and visitor vehicles.